骨の治癒がヒントに! 高速で傷が治る耐熱セラミックス
「自己治癒材料」とは
骨は我々の体重や日々の活動を支えている主要な構造部材です。さらに、骨折した場合、き裂を「自律的」、そして「完全」に修復してくれます。この機能は、室温、大気中および地球の重力下で人が持続的に活動していくために、進化の過程において最適化された機能であり、力学構造部材としての骨の寿命と信頼性を決定するとても大切な機能です。今、この「自己治癒」という生命体特有の機能を人工材料に発現しようという取り組みが世界中で活発化しています。
自己治癒の対象はどんな機能・性能であっても構いませんが、部材の寿命を決定するものであることが重要です。たとえば、骨やセラミックス等の力学構造部材の重要な性能は強度です。したがって、き裂発生によって劣化した強度を完全に回復させることが自己治癒の目的となります。一方、人の皮膚やスマートホンのコーティングは、外界からの保護機能、場合によっては見栄えの方が重要です。人によっては、まだまだ使えるのもかかわらず、表面に大きな傷があるという理由でスマートホンを交換または修理に出す場合もあると思います。この場合、寿命を決定する機能は「見栄え」であり、見栄えを完全に回復することが自己治癒の目的となります。
日本発! 自己治癒セラミックス
セラミックスは軽くて耐熱性に優れるため、次世代航空機エンジン用材料として注目されてきました。もし、エンジンのタービン静動翼をすべてセラミックスに置き換えることができれば、世界最高効率の航空機エンジンを開発可能になります。この様な耐熱材料の開発技術は、日本の航空産業復興のための最重要な要素技術であると共に、CO2排出量や燃料費削減にも大きく貢献します。
ただ、セラミックスは脆いという事実が、セラミックス製タービン動翼の実現を長い間阻んできました。これに対し、1995年に横浜国立大学の研究グループは、高温の使用環境でき裂を自然に修復できる「自己治癒セラミックス」を世界に先駆けて提案しました。このセラミックスは、酸化物であるアルミナの中に非酸化物である炭化ケイ素を複合したセラミックスで、高温環境下で表面に傷がつくと、炭化ケイ素が周囲の酸素と反応し、生成した酸化物が傷を自然に埋めることができます。
画期的な点は、「周囲の酸素」を治癒に活用したアイデアです。人の骨の自己治癒は、炎症・修復・改変期という3つの過程を経て、き裂を修復します。炎症期においては、「動く相」である血液が骨折した部位を充填し、その後の反応の足場を作るという大切な役割を担います。ただ、セラミックスが生きているのは高温環境です。初期構造に液相を配置してしまうと、高温強度が著しく低下するため、強度設計手法としてそもそも相応しくありません。この問題に対し、気相である酸素を「動く相」として活用し、化学反応の種を材料内部でなく外部に配置した発想の転換が、自己治癒セラミックスの画期的な特徴と言えます。
しかしながら、炭化ケイ素と酸素の反応を利用した場合、1000℃では、治癒時間が1000時間以上もかかってしまうという問題がありました。また、そもそも、酸化物がどのような過程で傷を埋めているのか? なぜ強度が完全に回復するか? 詳細なメカニズムはこれまでわかっていませんでした。
自己治癒メカニズムの解明
このような問題を解決するために、所属する物質・材料研究機構の最先端分析装置と蓄積したノウハウを用い、治癒メカニズムの解明に着手しました。まず、注目したのは、1200-1300℃付近で、酸化反応後にこれまでも観察されていた「水滴状」の酸化物の調査です。炭化ケイ素が酸化して生成する物質は二酸化ケイ素です。ただし二酸化ケイ素の融点は1700℃程度であり、なぜ水滴状なのか理由はわかっていませんでした。また、二酸化ケイ素の安定構造はガラス構造で、優れた高温強度を持つ物質ではありません。このため、すでに実証されていた自己治癒セラミックスの優れた高温強度を説明することができていませんでした。
これらを解決するため、透過型電子顕微鏡を用い、治癒部の詳細な観察を実施しました。その結果、治癒部には二酸化ケイ素と母材であるアルミナが反応している証拠を発見することに成功しました。これにより、「水滴状」の酸化物は、ニ酸化ケイ素とアルミナが反応し生成した「過冷却融体」と言われる粘性の低いガラス相であることがわかりました。自己治癒セラミックスにおいて、「動く相」は酸素のみと長年考えられてきました。本研究により、もうひとつの動く相である過冷却融体の生成が、き裂治癒の重要な素過程であることが分かりました。さらに、一時的に生成した過冷却融体は、最終的には高温強度に優れる結晶相に変化していることも確認されました。
一連の治癒過程は、炎症・修復・改変期を通した骨の治癒過程にとてもよく似ています。骨折が起こると、炭化ケイ素の酸化が誘発されます。これは炎症期に対応します。さらに生成したニ酸化ケイ素は周囲のアルミナと反応し過冷却融体を生成し、3次元的で複雑なき裂の体積を隅々まで埋めていきます。これは炎症・修復期に対応しています。さらに、過冷却融体は結晶化し強固な結晶を生成します。これは改変期の一部に対応しています。
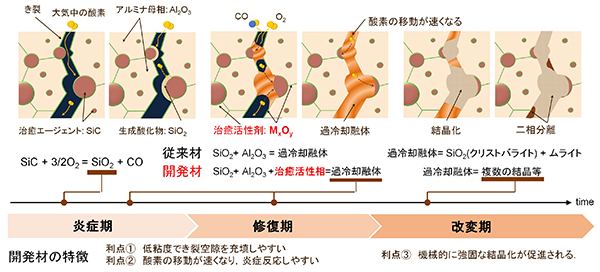
骨の治癒がヒントに – 治癒活性相3Dネットワークの設計
ただ、観察だけでは完全な解明とは言えません。次に血液のような役割を果たす過冷却融体の設計に着手しました。熱力学平衡計算を駆使し、周期表上でアルミナと同じ役割を果たし、酸化物の粘性を一時的に低下させる、「治癒活性相」の探索を実施しました。その結果、たとえば1000℃で治癒を活性化させる相として酸化マンガンを見出しました。
次に酸化マンガンの有効な配置場所の設計を行いました。酸化マンガンの添加が強度や靱性といった重要な機械的特性を著しく損なってしまってはなりません。できるだけ少ない量で、できるだけ効率良く、き裂のどの場所でも、しっかりと反応に寄与するように工夫が必要でした。そこでヒントにしたのが、骨の中に存在する骨細胞と体液輸送ネットワークです。治癒活性相も3Dネットワーク上に配置しました。また、き裂の進展経路となるアルミナの粒界や炭化ケイ素の界面に局在化させることで、酸化マンガンが損傷部に必ず濃化するように設計しました。
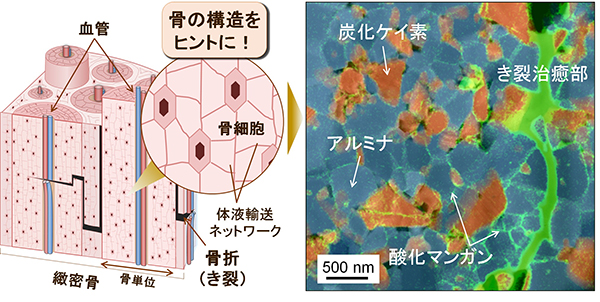
フライト中に傷を治す!? 夢の航空機エンジン
このような設計手法のもと、従来材であるアルミナ/炭化ケイ素複合材に、酸化マンガンを0.2から1.0体積%添加した試験片を作製し、治癒速度を測定しました。この結果、従来材よりも最大で6万倍高速、最速1分でき裂を完治することに成功しました。この瞬間が、観察で見いだされていた骨のような治癒機構が実証された瞬間です。
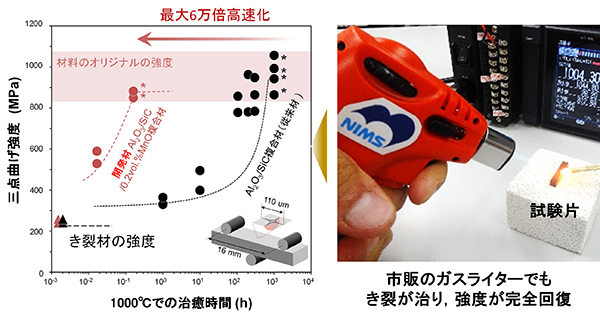
今回記録した1分という治癒時間は、航空機のフライト時間よりも十分短い時間です。たとえば東京の羽田空港から北海道の新千歳空港までの巡航時間は1時間程度です。したがって、セラミックス自身が、フライト中に発生した微細なき裂をその場で治癒し、着陸に備えることができるようになるための大きな一歩であると考えています。骨自体も脆い材料で構成されています。にもかかわらず、き裂を治癒することで高い信頼性を有しています。人の骨の持つ治癒能力を適切にセラミックスに移植することで、セラミックスは脆いという常識を打破できると我々は確信しています。身近な自然から学ぶこと、そして我々の目の前にある骨の治癒から学ぶことこそが、実は日本が直面しているさまざまな問題解決の一番の近道かもかもしれません。
参考文献
- T. Osada, K. Kamoda, M. Mitome, T. Hara, T. Abe, Y. Tamagawa, W. Nakao, T. Ohmura, “A Novel Design Approach for Self-Crack-Healing Structural Ceramics with 3D Networks of Healing Activator”, Scientific Reports. 7 (2017) 17853-1, DOI: 10.1038/s41598-017-17942-6.
- T. Osada, W. Nakao, K. Takahashi, K. Ando. “Self-crack-healing behavior in ceramic-matrix composites”, Advances in ceramics matrix composites, (2014), 410, DOI: 10.1533/9780857098825.2.410
- 長田 俊郎, 尾崎伸吾, 中尾航. 自己治癒セラミックスにおける速度論モデルの最新動向. Journal of the Society of Inorganic Materials, Japan. 23 [385] (2016) 460
この記事を書いた人
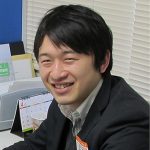
-
国立研究開発法人 物質・材料研究機構(NIMS) 構造材料研究拠点 主任研究員。
2009年3月横浜国立大学工学府機能発現工学専攻修了 博士(工学)取得。同4月よりNIMS超耐熱材料 NIMSセンターポスドク研究員。2012年1月より横浜国立大学 特任教員(研究教員)。2013年4月よりNIMS研究員、2016年3月よりデルフト工科大学(オランダ)客員研究員を経て現在に至る。
この投稿者の最近の記事
研究成果2018.04.12骨の治癒がヒントに! 高速で傷が治る耐熱セラミックス